Aniloks silindir hücrelerinin tıkanması aslında aniloks silindirlerin kullanımında en kaçınılmaz konudur. Belirtileri iki duruma ayrılır: aniloks silindirin yüzey tıkanması (Figür.1) ve aniloks silindir hücrelerinin tıkanması (Figür. 2).
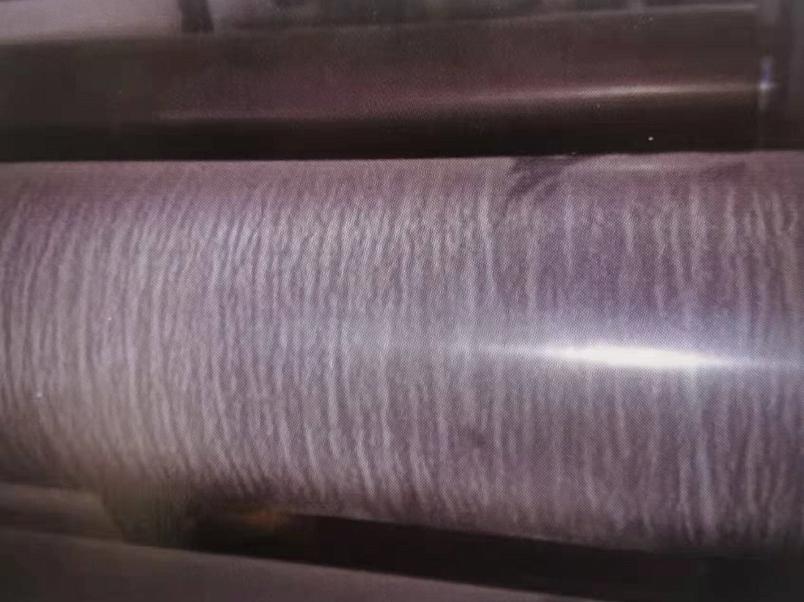
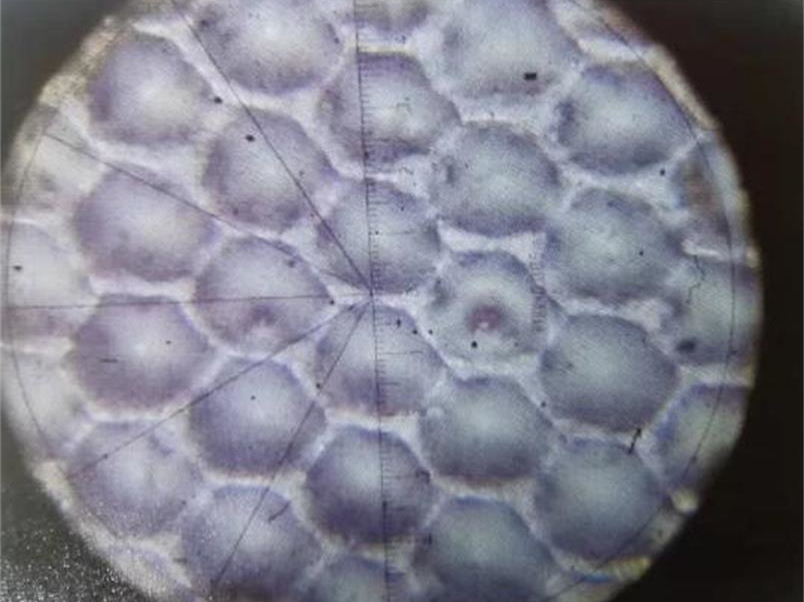
Şekil .1
Şekil .2
Tipik bir flekso mürekkep sistemi, bir mürekkep haznesi (kapalı mürekkep besleme sistemi), aniloks silindiri, plaka silindiri ve alt tabakadan oluşur. Yüksek kaliteli baskılar elde etmek için mürekkep haznesi, aniloks silindiri hücreleri, baskı plakası noktalarının yüzeyi ve alt tabakanın yüzeyi arasında istikrarlı bir mürekkep transfer süreci oluşturmak gerekir. Bu mürekkep transfer yolunda, aniloks silindirinden plaka yüzeyine mürekkep transfer oranı yaklaşık %40'tır. Plakadan alt tabakaya mürekkep transferi yaklaşık %50'dir. Böyle bir mürekkep yolu transferinin basit bir fiziksel transfer değil, mürekkep transferi, mürekkebin kuruması ve mürekkebin yeniden çözülmesini içeren karmaşık bir süreç olduğu görülebilir; Flekso baskı makinesinin baskı hızı gittikçe arttıkça, bu karmaşık süreç yalnızca daha da karmaşık hale gelmeyecek, aynı zamanda mürekkep yolu iletimindeki dalgalanmaların sıklığı da gittikçe artacaktır; Deliklerin fiziksel özelliklerine yönelik gereksinimler de giderek artmaktadır.
Çapraz bağlama mekanizmasına sahip polimerler, poliüretan, akrilik reçine vb. mürekkeplerde, mürekkep tabakasının yapışmasını, aşınma direncini, su direncini ve kimyasal direncini artırmak için yaygın olarak kullanılır. Aniloks silindir hücrelerindeki mürekkep transfer oranı yalnızca %40 olduğundan, hücrelerdeki mürekkebin çoğu aslında tüm baskı işlemi boyunca hücrelerin dibinde kalır. Mürekkebin bir kısmı değiştirilse bile, mürekkebin hücrelerde tamamlanmasına neden olmak kolaydır. Reçine çapraz bağlaması, alt tabakanın yüzeyinde gerçekleşir ve bu da aniloks silindir hücrelerinin tıkanmasına yol açar.
Aniloks merdanesinin yüzeyinin tıkalı olduğunu anlamak kolaydır. Genellikle aniloks merdaneleri yanlış kullanılır, bu nedenle mürekkep aniloks merdanesinin yüzeyinde kürlenir ve çapraz bağlanır, bu da tıkanıklığa neden olur.
Aniloks rulo üreticileri için, seramik kaplama teknolojisinin araştırma ve geliştirmesi, lazer uygulama teknolojisinin iyileştirilmesi ve aniloks rulolarının gravürlenmesinden sonra seramik yüzey işleme teknolojisinin iyileştirilmesi, aniloks rulo hücrelerinin tıkanmasını azaltabilir. Günümüzde yaygın olarak kullanılan yöntemler, ağ duvarının genişliğini azaltmak, ağın iç duvarının pürüzsüzlüğünü artırmak ve seramik kaplamanın kompaktlığını artırmaktır.
Baskı işletmeleri için mürekkebin kuruma hızı, çözünürlüğü ve rakle noktasından baskı noktasına olan mesafe de ayarlanabilmekte, böylece aniloks silindir hücrelerinin tıkanması azaltılabilmektedir.
Korozyon
Korozyon, Şekil 3'te görüldüğü gibi, aniloks silindirin yüzeyinde noktasal çıkıntıların oluşması olayıdır. Korozyon, temizleme maddesinin seramik boşluk boyunca alt tabakaya sızması, alt metal taban silindirini aşındırması ve seramik tabakayı içeriden kırarak aniloks silindire zarar vermesiyle oluşur (Şekil 4, Şekil 5).
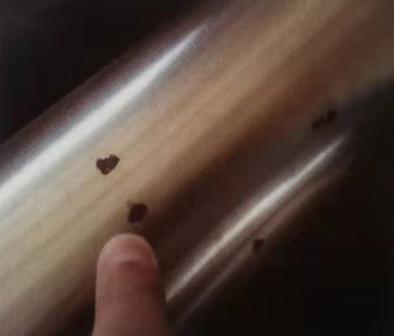
Şekil 3
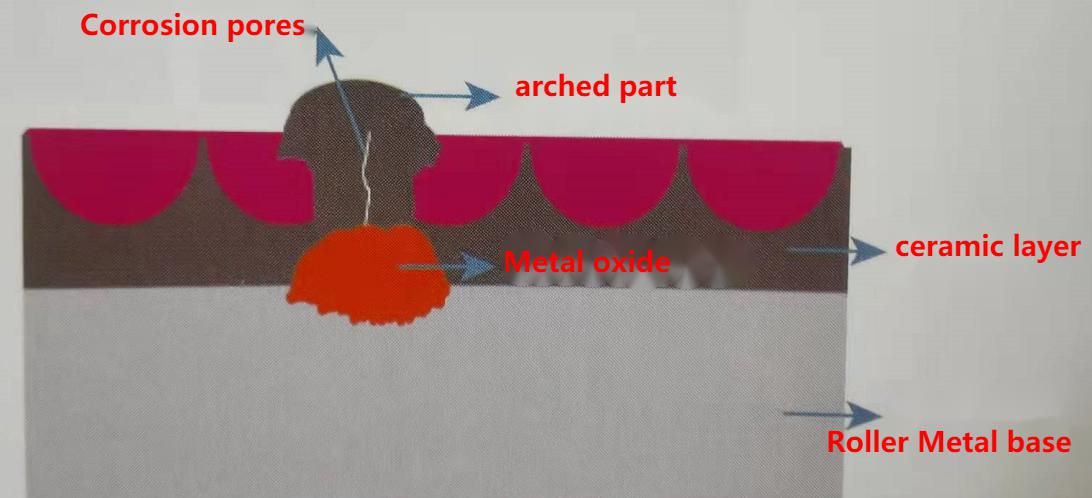
Şekil 4
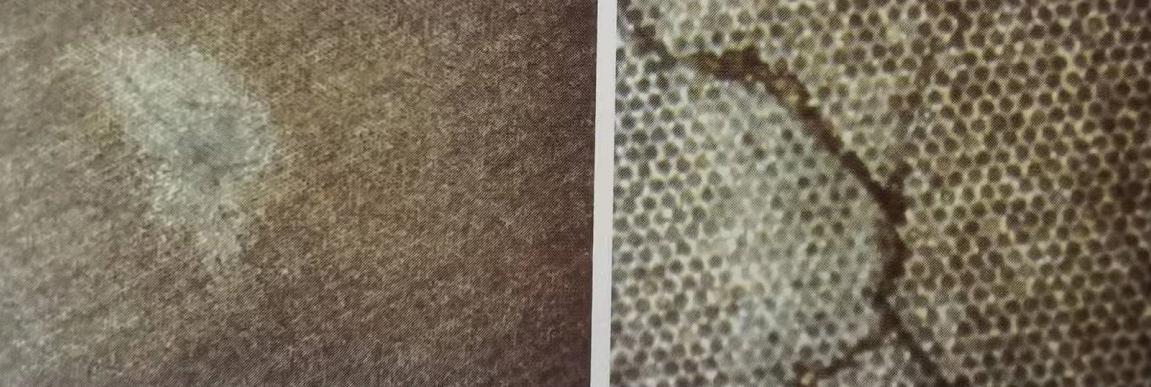
Şekil 5 Mikroskop altında korozyon
Korozyonun oluşum nedenleri şunlardır:
① Kaplamanın gözenekleri büyüktür ve sıvı gözenekler yoluyla taban silindirine ulaşabilir ve taban silindirinin aşınmasına neden olabilir.
② Güçlü asitler ve güçlü alkaliler gibi temizlik maddelerinin uzun süreli kullanımı, kullanımdan sonra zamanında duş alınmaması ve hava ile kurutulmaması.
③ Özellikle ekipmanların uzun süre temizlenmesinde, temizleme yöntemi yanlıştır.
④ Depolama yöntemi yanlıştır ve uzun süre nemli ortamda saklanmıştır.
⑤ Mürekkebin veya katkı maddelerinin pH değeri, özellikle su bazlı mürekkebin pH değeri çok yüksektir.
⑥ Aniloks merdane, montaj ve demontaj işlemi sırasında darbe alır ve bunun sonucunda seramik katman boşluğu değişir.
Korozyonun başlaması ile aniloks silindirinin hasar görmesi arasındaki uzun süre nedeniyle, ilk işlem genellikle gözden kaçar. Bu nedenle, seramik aniloks silindirinde torbalanma sorununu tespit ettikten sonra, arkın nedenini araştırmak için seramik aniloks silindir tedarikçisiyle zamanında iletişime geçmelisiniz.
Çevresel çizikler
Aniloks merdanelerin ömrünü etkileyen en yaygın sorunlardan biri de aniloks merdane çizikleridir.(şekil 6)Bunun nedeni, aniloks merdanesi ile doktor bıçağı arasındaki parçacıkların, basınç etkisi altında aniloks merdanesinin yüzey seramiklerini kırması ve baskı yönündeki tüm gözenek duvarlarını açarak bir oluk oluşturmasıdır. Baskıdaki performans, daha koyu çizgilerin ortaya çıkmasıdır.
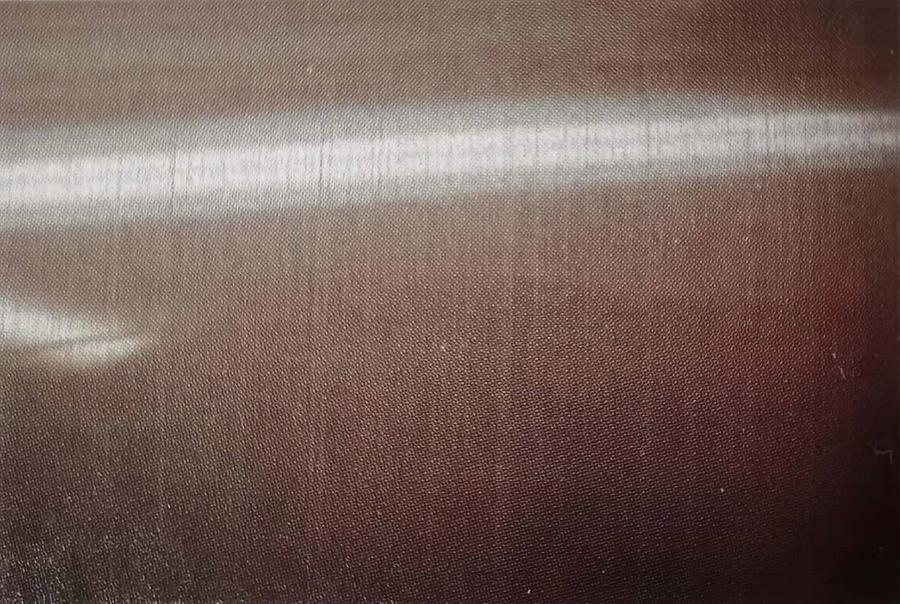
Şekil 6 Çizikli aniloks rulosu
Çiziklerin temel sorunu, doktor bıçağı ile aniloks silindiri arasındaki basıncın değişmesidir; böylece orijinal yüzey basıncı, yerel nokta-yüzey basıncı haline gelir; ve yüksek baskı hızı, basıncın keskin bir şekilde artmasına neden olur ve yıkıcı güç şaşırtıcıdır. (Şekil 7)
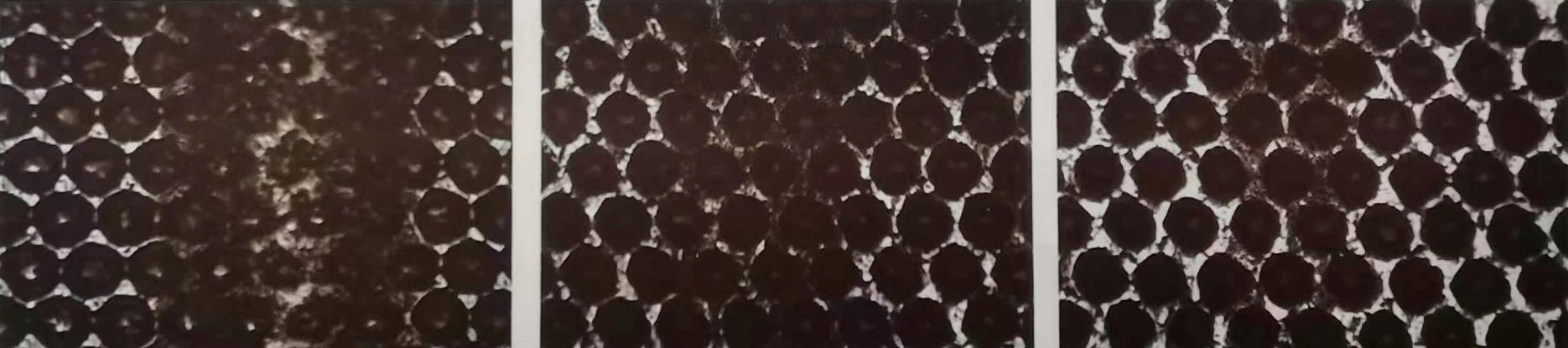
Şekil 7 ciddi çizikler
Genel çizikler
küçük çizikler
Genellikle baskı hızına bağlı olarak, baskıyı etkileyen çizikler 3 ila 10 dakika içinde oluşur. Bu basıncı değiştiren birçok faktör vardır; özellikle aniloks silindirin kendisi, doktor bıçağı sisteminin temizliği ve bakımı, doktor bıçağının kalitesi, kurulumu ve kullanımı ve ekipmanın tasarım kusurları.
1. aniloks silindiri kendisi
(1) Seramik aniloks silindirin yüzey işlemi gravürden sonra yeterli değildir ve yüzey pürüzlüdür ve kazıyıcı ve kazıyıcı bıçağı tarafından çizilmesi kolaydır.
Aniloks merdane ile temas yüzeyi değişmiş, basınç artmış, basınç katlanmış ve yüksek hızlı çalışma durumunda ağ kopmuştur.
Kabartmalı silindirin yüzeyinde çizikler oluşuyor.
(2) Parlatma ve ince taşlama işlemi sırasında derin bir parlatma çizgisi oluşur. Bu durum genellikle aniloks rulosu teslim edildiğinde ortaya çıkar ve hafif parlatma çizgisi baskıyı etkilemez. Bu durumda, baskı doğrulamasının makinede yapılması gerekir.
2.Doktor bıçağı sisteminin temizliği ve bakımı
(1) Hazne doktor bıçağının seviyesi düzeltilse bile, seviyesi düşük bir hazne doktor bıçağı eşit olmayan basınca neden olur. (Şekil 8)
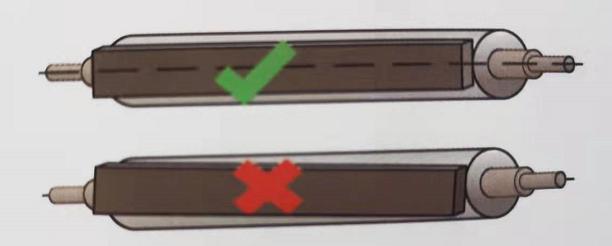
Şekil 8
(2) Doktor bıçağı haznesi dikey tutulsa bile, dikey olmayan mürekkep haznesi bıçağın temas yüzeyini artıracaktır. Ciddi olarak, aniloks silindirine doğrudan zarar verecektir. Şekil 9
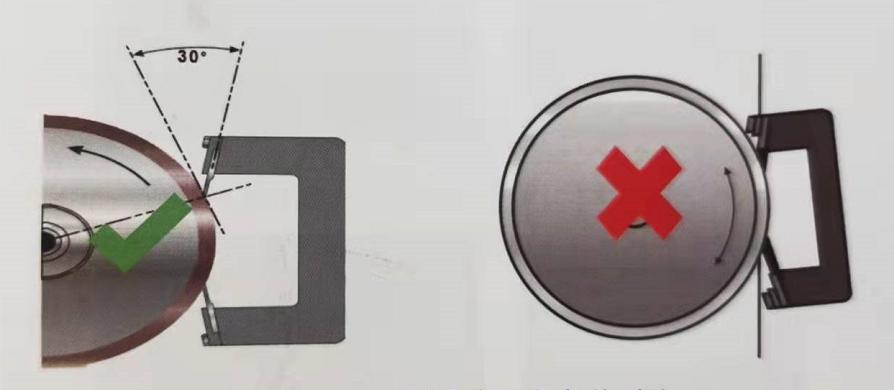
Şekil 9
(3) hazneli doktor bıçağı sisteminin temizliği çok önemlidir. Doktor bıçağı ile aniloks silindiri arasında sıkışan kirleticilerin mürekkep sistemine girmesini ve basınçta değişikliklere neden olmasını önleyin. Kuru mürekkep de çok tehlikelidir.
3.Doktor bıçağının montajı ve kullanımı
(1) Bıçağın hasar görmemesini, bıçağın dalgalar olmadan düz olmasını ve bıçak tutucusuyla mükemmel bir şekilde birleşmesini sağlamak için hazne doktor bıçağını doğru şekilde takın, örneğin:
Şekil 10’da görüldüğü gibi aniloks merdanenin yüzeyindeki basıncın eşit olmasına dikkat edilmelidir.
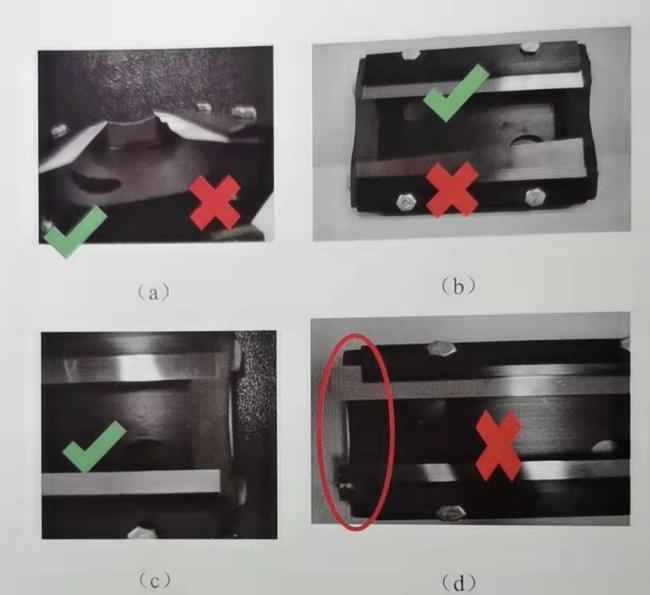
Şekil 10
(2) Yüksek kaliteli kazıyıcılar kullanın. Yüksek kaliteli kazıyıcı çeliğin, Şekil 11 (a)'da gösterildiği gibi, aşınmadan sonra sıkı bir moleküler yapısı vardır. Parçacıklar küçük ve düzgündür; düşük kaliteli kazıyıcı çeliğin moleküler yapısı yeterince sıkı değildir ve parçacıklar, Şekil 11 (b)'de gösterildiği gibi aşınmadan sonra büyüktür.
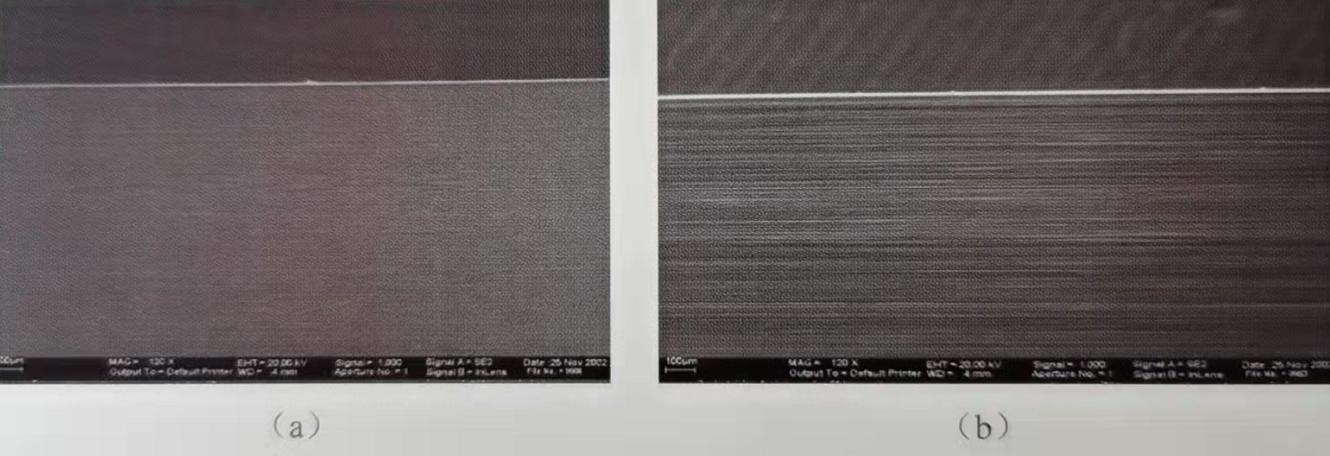
Şekil 11
(3) Bıçak bıçağını zamanında değiştirin. Değiştirirken, bıçak ağzının darbe almasını önlemeye dikkat edin. Aniloks silindirinin farklı bir sıra numarasını değiştirirken, bıçak bıçağını da değiştirmeniz gerekir. Şekil 12'de gösterildiği gibi, farklı sıra numaralarına sahip aniloks silindirinin aşınma derecesi tutarsızdır; soldaki resim, düşük sıra numarası ekranıdır. Bıçak bıçağının bıçak bıçağı üzerinde taşlanması. Hasarlı uç yüzeyinin durumu; sağdaki resim, yüksek sıra sayılı aniloks silindirinin bıçak bıçağına aşınmış uç yüzeyinin durumunu göstermektedir. Aşınma seviyeleri uyumsuz olan doktor bıçağı ile aniloks silindiri arasındaki temas yüzeyi değişerek basınç değişikliklerine ve çiziklere neden olur.
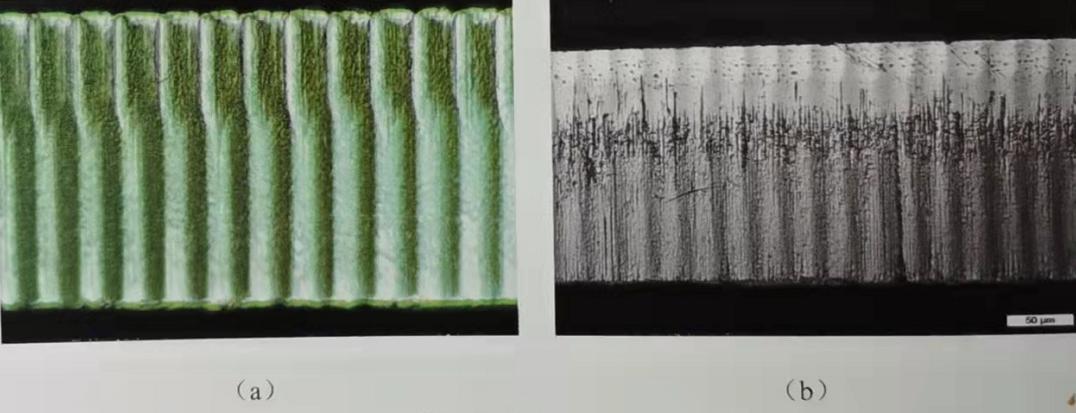
Şekil 12
(4) Raklenin basıncı hafif olmalı ve raklenin aşırı basıncı, Şekil 13'te gösterildiği gibi, rakle ile aniloks silindirinin temas alanını ve açısını değiştirecektir. Kirleticilerin içeri girmesi kolaydır ve içeri giren kirleticiler, basınç değiştirildikten sonra çiziklere neden olur. Aşırı basınç kullanıldığında, değiştirilen kazıyıcının kesitinde aşınmış metal uçlar oluşur (Şekil 14). Kazıyıcı düştüğünde, kazıyıcı ile aniloks silindiri arasına sıkışır ve bu da aniloks silindirinde çiziklere neden olabilir.
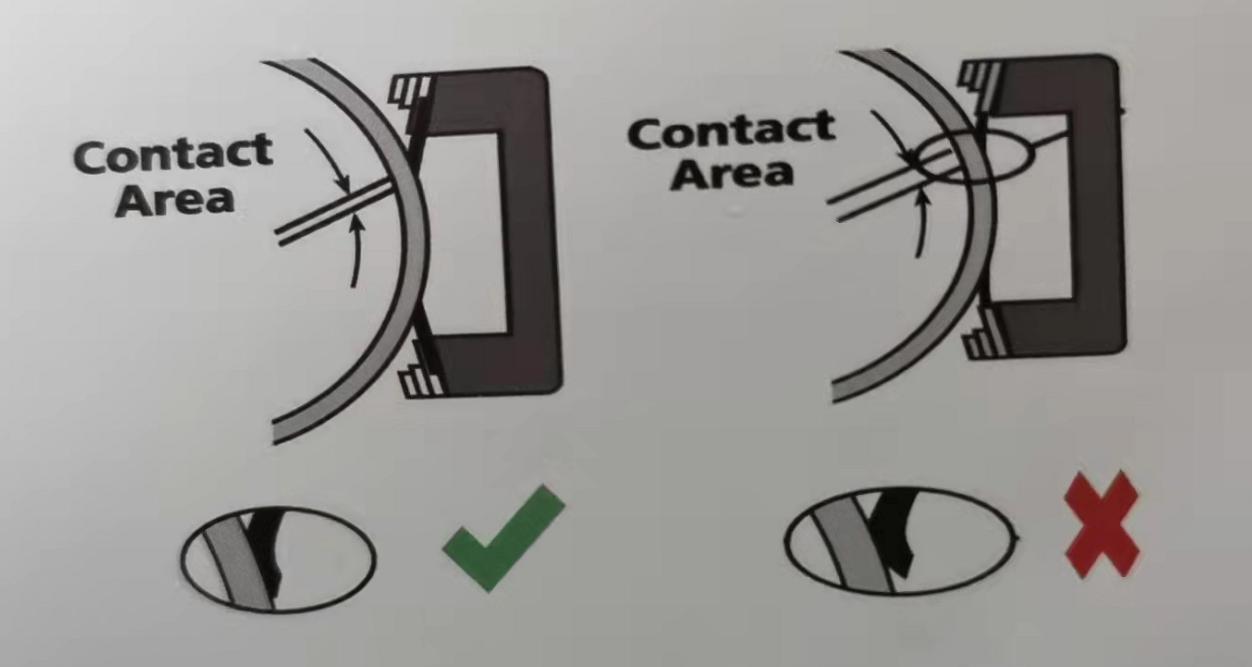
Şekil 13
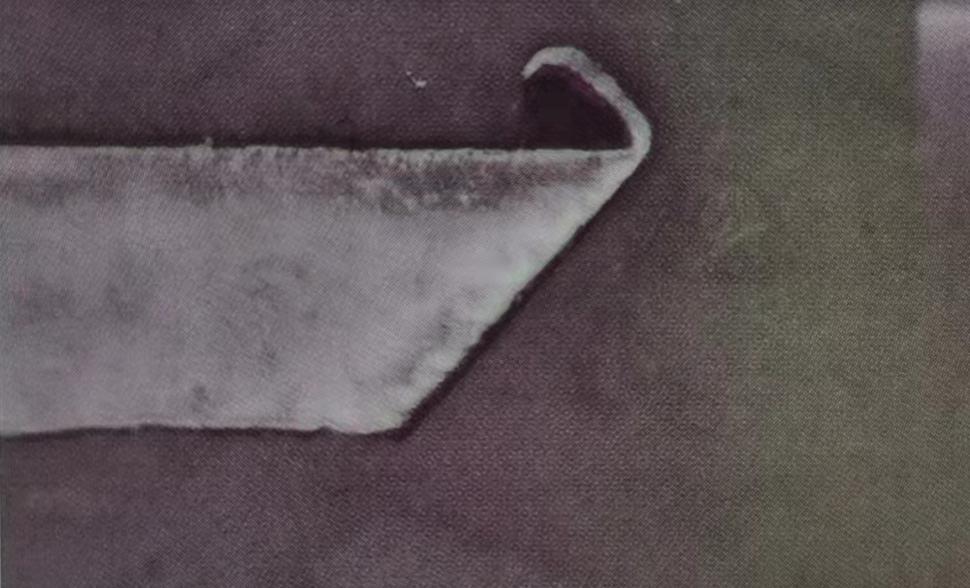
Şekil 14
4. ekipmanın tasarım kusurları
Mürekkep bloğunun tasarımı ile aniloks silindirinin çapı arasındaki uyumsuzluk gibi tasarım kusurları da kolayca çizik oluşumuna neden olabilir. Rakle açısının mantıksız tasarımı, aniloks silindirinin çapı ve uzunluğu arasındaki uyumsuzluk vb. belirsiz faktörler ortaya çıkaracaktır. Aniloks silindirinin çevresel yönündeki çizik sorununun oldukça karmaşık olduğu görülebilir. Basınç değişikliklerine dikkat etmek, zamanında temizlik ve bakım yapmak, doğru sıyırıcıyı seçmek ve iyi ve düzenli çalışma alışkanlıkları, çizik sorununu büyük ölçüde azaltabilir.
Çarpışma
Seramikler sertliği yüksek olmasına rağmen kırılgan malzemelerdir. Dış kuvvetlerin etkisiyle seramikler kolayca düşebilir ve çukurlar oluşturabilir (Şekil 15). Genellikle aniloks silindirleri yüklenirken ve boşaltılırken darbeler oluşur veya metal aletler silindir yüzeyinden düşer. Baskı ortamını temiz tutmaya çalışın ve özellikle mürekkep tepsisi ve aniloks silindiri yakınında olmak üzere baskı makinesinin etrafına küçük parçalar yığmaktan kaçının. İyi bir aniloks baskısı yapmanız önerilir. Küçük nesnelerin düşüp aniloks silindirine çarpmasını önlemek için silindirin uygun şekilde korunması önerilir. Aniloks silindiri yüklenirken ve boşaltılırken, çalıştırmadan önce esnek bir koruyucu örtü ile sarılması önerilir.
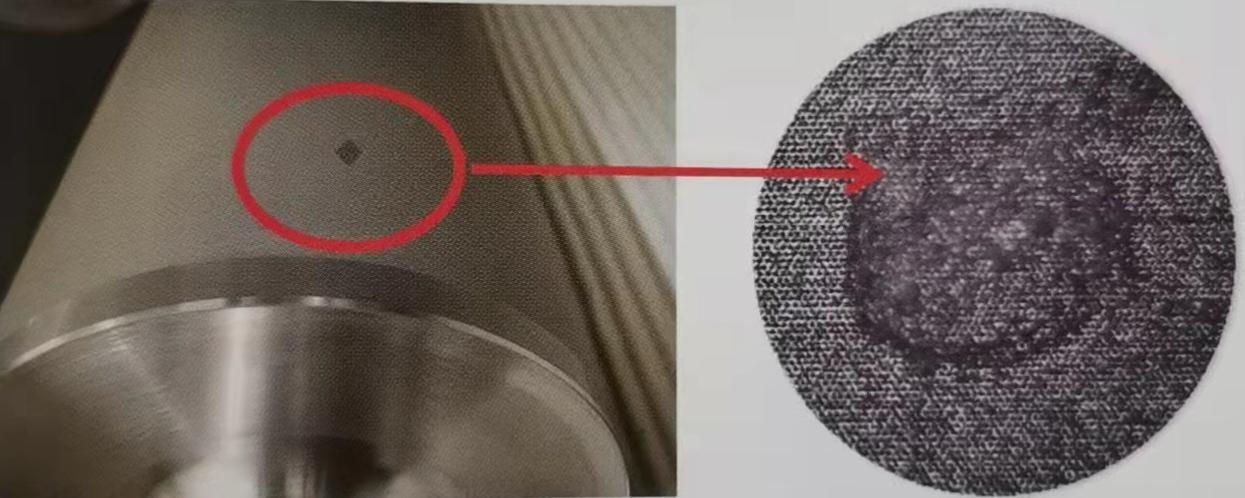
Şekil 15
Gönderim zamanı: 23 Şubat 2022